Paragraph
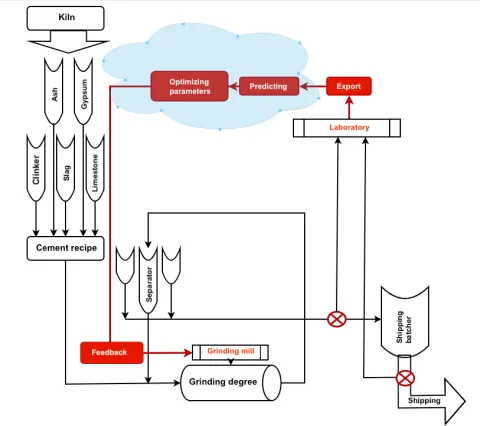
Model training thanks to impact: Econcrete model is trained based on values that already exist in the cement plant. In addition to the chemical and mineralogical properties, this also includes the results achieved, such as the strength after curing for one to 30 days.
Strength prediction: Just as the properties and qualities of natural resources fluctuate, all fluctuations (mineralogy, chemical formula, real particle size distribution ) must also be taken into account and compensated for by correct control when producing homogeneous and qualitatively stable cement. Our models predict quality properties such as compressive strength and Blaine of the current grind or blend. This means that the fluctuations in resources are not only visible in the raw data, but also in the target values.
Optimization: However, it does not just remain with the pure strength prediction, but the technology uses the knowledge gained to create control specifications for the cement mill for the current production and to find optimal target values for fineness or the right recipe to achieve the desired target properties. These are then transmitted to the control room operator or imported directly into the process control system.
The result: Less fluctuation in concrete robustness.
Econcrete - integrated technology of concrete production and transportation management
Paragraph
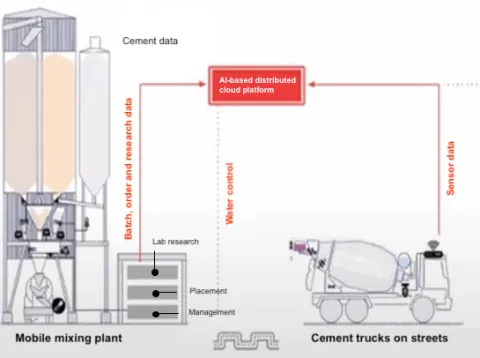
- According to the data on cement mix and component humidity (sand, gravel) we correct the water volumes added to reach our target concrete robustness.
- Concrete mix control with IIoT sensors.
The result: precise and predictable robustness of the mixed concrete
Paragraph
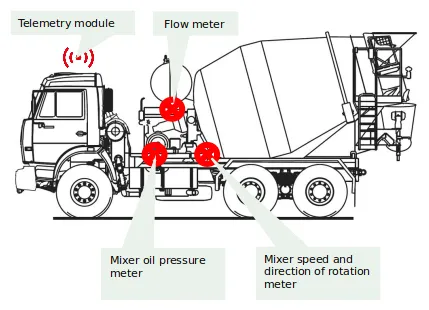
The final progress expected (based on world’s best practices):
- 100% production management and predictable quality
- 40% more stable cement and concrete production
- 80% less hand work in cement and concrete production
- 50% less CO2 due to clinker reduce
- 35% higher cement quality thanks to using silica fume
- 20-30% cost impact (based on world’s best practices)
- 1000 roubles (more than 10 USD) of savings per 1 ton of cement